
Figure 1. Lindosland. (2009). ITU-R 468 graph, A weighting, ISO 226 inverse, showing that A-weighting is similar to the equal loudness curves of human hearing for sine tones. Public Domain. Retrieved from https://commons.wikimedia.org/wiki/File:Lindos3.svg
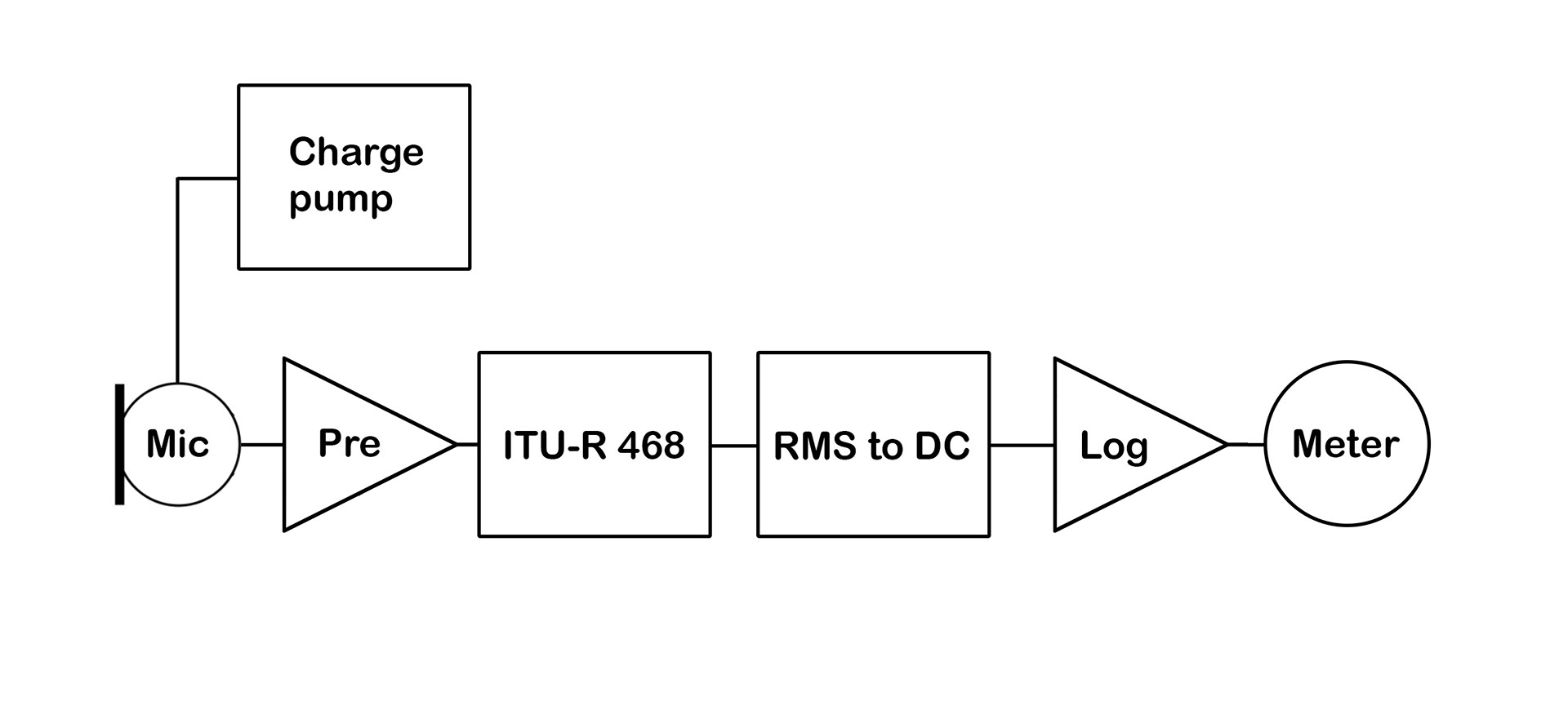
Figure 2: Block diagram of the sound level meter
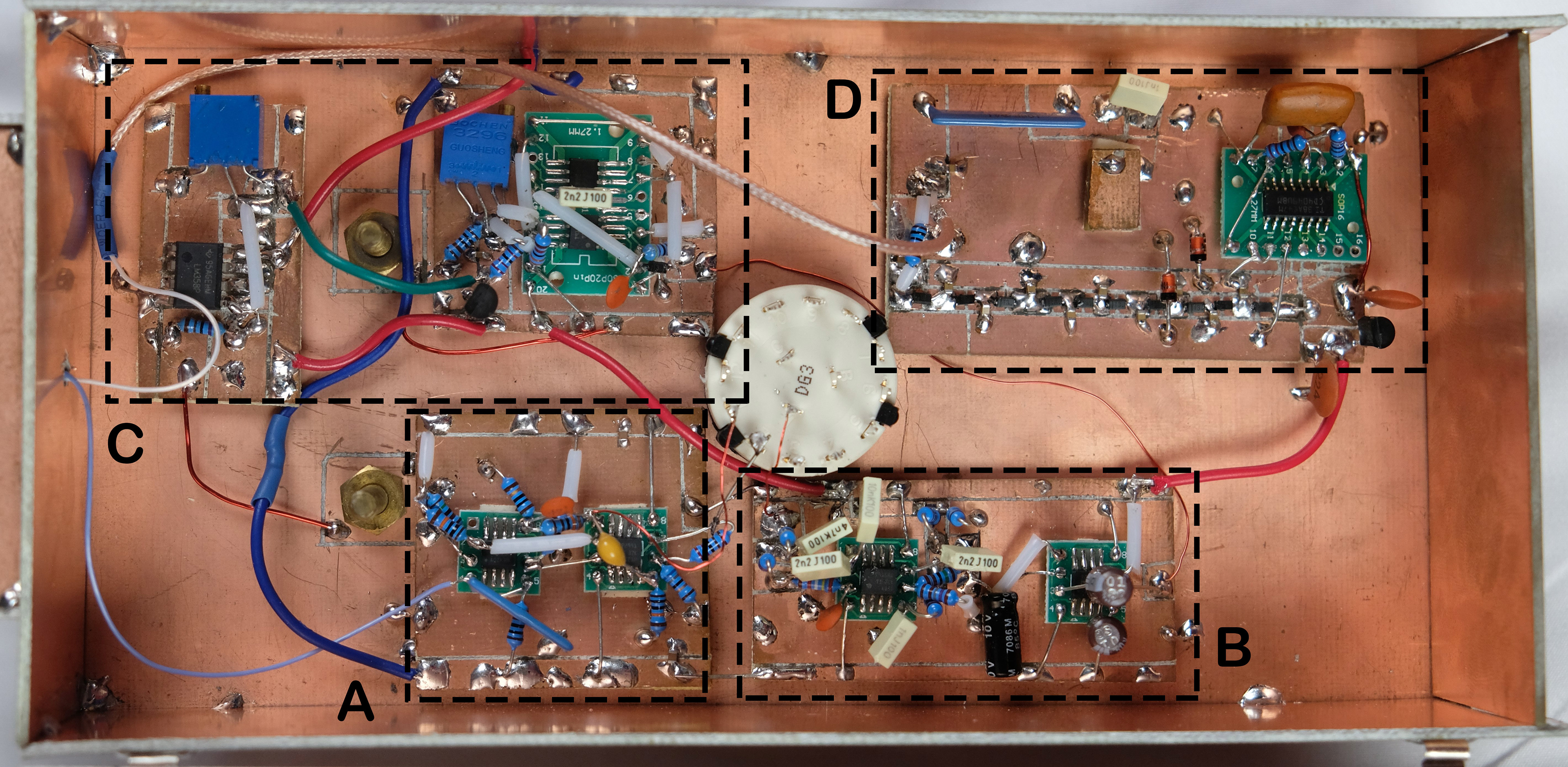
Figure 3: Sound level meter hardware implementation showing A) preamplifier; B) weighting filter and RMS-DC; C) log amplifier and meter circuitry; D) charge pump
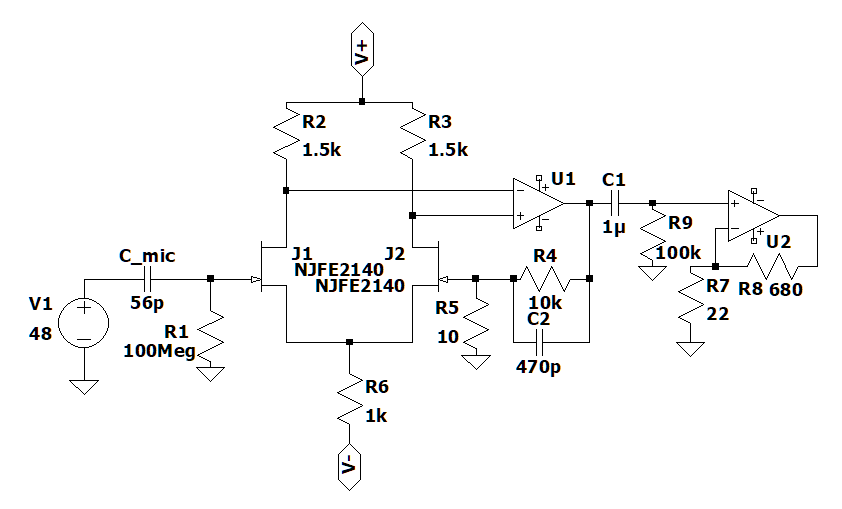
Figure 4: Preamplifier schematic
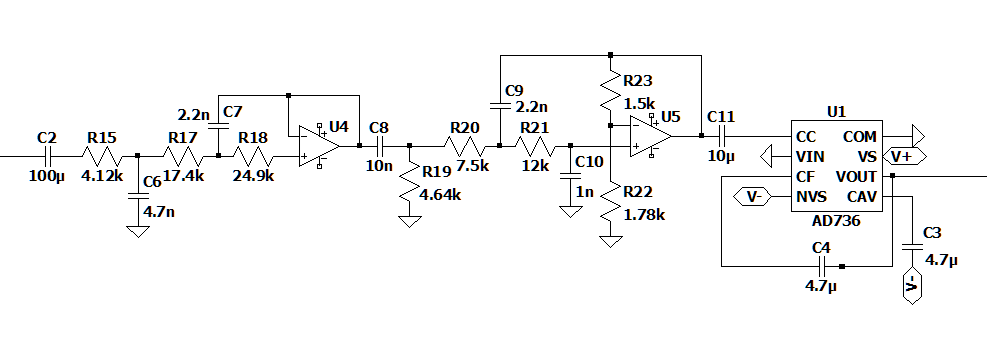
Figure 5: Weighting filter and RMS-DC converter. Beis, Ewe. "Weighting Filter Set." October 2015. Web. 25 Apr. 2024. <https://www.beis.de/Elektronik/AudioMeasure/WeightingFilters.html>.
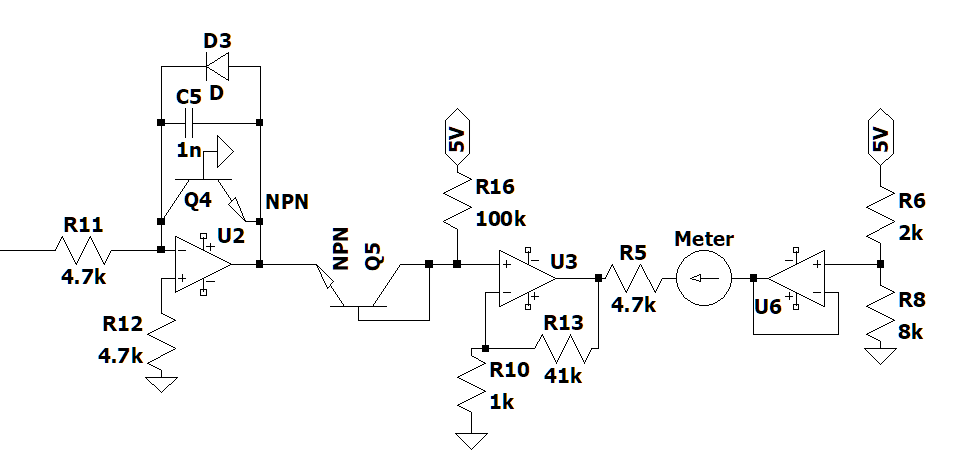
Figure 6: Log amp and meter conditioning
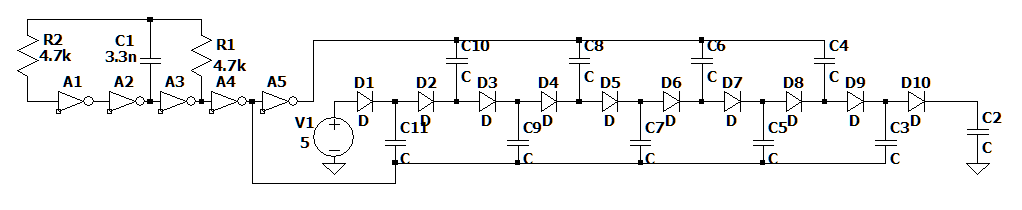
Figure 7: Dickson charge pump